The Inventive Life of Charles Hill Morgan: The Power of Improvement In Industry, Education and Civic Life. Allison Chisolm
Чтение книги онлайн.
Читать онлайн книгу The Inventive Life of Charles Hill Morgan: The Power of Improvement In Industry, Education and Civic Life - Allison Chisolm страница 15
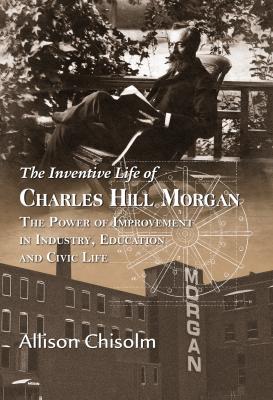
Hiram Morgan’s house in Clinton, Massachusetts
While there are no surviving diary entries for the year 1856, Charles probably continued his work with Parker’s growing business. He did leave a notebook created that year filled with his own ideas for a paper bag machine that would have a better design than Smith’s or Goodale’s and could be commercially viable.
GENIUS AND GOOD MANAGEMENT
Charles Morgan returned to the Bigelow fold in March 1857, as his diary recorded, when he “commenced work for E.B. Bigelow making drawings of Brussels Carpet Loom Improvements.” At 26, Morgan had finally found in Erastus Bigelow the creative mentor capable of helping him refine his own ideas and improvements on existing machines.
Bigelow relied on skilled draftsmen, as he admitted some time earlier to a colleague, as an essential part of his own inventing process.
I always mature in my mind the general plan of an invention before attempting to execute it, resorting occasionally to sketches on paper for the more intricate parts. A draughtsman prepares the working drawings from sketches furnished by me, which indicates in figures the proportion of the parts. I never make anything with my own hands. I do not even like drawing to scale.
Bigelow had built his career and several flourishing businesses around his inventions, his patents on those inventions and, although somewhat controversial for his time, their value on his companies’ balance sheets. His four main patents equipped him to boost productivity, compete effectively with foreign producers and introduce higher quality carpeting to the American market: First, the coach lace loom, as described earlier; counterpane looms, to produce quilted coverlets; gingham looms, which launched the Lancaster Mills; and through the 1850s, Brussels looms. His efforts as both manufacturer and consummate salesman enabled the Bigelow name to represent quality and product leadership.
His patents were robust enough to pose an insurmountable barrier to entry for competitors until well after the Civil War. His Brussels carpet loom and two types of English looms were the only ones operating in the U.S. and Bigelow did not license his machines to other companies. This control of production kept prices high. Those who did not want a Bigelow carpet made in Clinton had to import theirs from England. As the newest business in the Bigelow empire, the Bigelow Carpet Company had plenty of growth plans. The previous year’s Clinton Almanac noted its capitalization of $200,000 and its production “annually about 210,000 yards of Velvet, Tapestry and Brussels carpeting of the most beautiful patterns and desirable materials. These mills... are propelled by steam power...some 150 persons on average, find employment.”
Within about two months of starting his work there, Morgan noted Bigelow’s request for help in another area of the business that needed new ideas and clear drawings to illustrate those ideas—tapestry carpet looms. Morgan soaked up every detail he could about the development of new looms, even correcting his diary notations as necessary, as he did in September 1857:
Note Mr. E.B.B. says use the same Take up ratchet gear as is used on Velvet Loom for the Velvet Tapestry*
*This was found to be wrong because there were 4 beats of the Loom the old Wilton & but 3 in the Improved Loom
He copied Bigelow’s “Sketch of Cam movements of Wire Parallel Lever & Wire Motion Shaft,” with column notations for each cam working either the lever or the shaft. In a typical entry, he listed each step of the wire loom’s weaving movements:
Wire supposed to be laid home
Move back Staff 2 inches
Rock the carrier back 3 ½ inches
Rest to engage wire
Staff to draw wire 27 ½ inches
Rest one beat
Rock forward 7 ½ inches
Staff insert wire 29 ½ inches
Rock back to fill
It was not surprising to imagine Charles perceiving alternative ways to design and run the looms. Working with Bigelow, his ideas would have been welcomed, rather than shrugged off as experimental and unproductive.
In a paper presented more than 20 years later at the Worcester County Free Institute, Morgan drew on his experiences working with Bigelow to address “Cam Construction.” He explained that “a cam is a mechanical device by means of which a velocity ratio, either constant or variable, is developed between two parts of a machine.” It can be understood as “an acting surface wrapped about an axis.” In other words, he wrote, “we shall consider the cam a disk.”
“Cam motions are often exceedingly perplexing,” he wrote, “and some system is especially perquisite in dealing with them.” He went on to say that cams and lay cranks “are developed by a single line of action.”
By May 1858, Morgan had fully comprehended the rhythm of cams, and developed his “Proposed Circle of Cam movements for gaining 30 percent of speed on Coach Lace Looms.” His overall theory was to use the full circle of cam movements to increase speed. In one diary entry, Morgan notes “Cam movements for 2 ft. wire Loom—circle of movements divided into 152 parts,” which would offer 152 locations for interactions with other parts of the loom system. But with speed can come destructive shock to the system, Morgan explained in his paper. One solution, the crank-motion cam, reduces shock significantly.
“But the question still arises,” he wrote, “can a body be lifted through a given space in the shortest possible time by its use, without shock? That is, have we arrived at the acme in cam making?”
There was always room for improvement, as Morgan’s mentors Bigelow and Parker would have agreed. Morgan proposed a pendulum motion in cam construction which would use the force of gravity to smooth out the uneven acceleration rates found with the crank motion cam. The addition of a friction roll, he explained, would help create a more efficient apparatus.
Also in 1858, Morgan and his business partner Benjamin R. Smith began to produce and sell paper bags using the machine patented by Benjamin F. Rice, as described in the next chapter.
The following year, Bigelow’s Wire Cloth Company began expanding its operations, and Morgan’s diary entries increasingly refer to Wire Looms. Rice was the chief machinist for the Wire Cloth Company, which was the first to successfully manufacture wire cloth by power in 1856. Their products were used for window screens, corn poppers, sieve bottoms and other applications. But with only a handful of employees, the mill did not yet have its own machine shop. This work and his contacts from it would prove fruitful for Morgan’s future in the metals industry.
PREPARED FOR NEW CHALLENGES
Charles Morgan was fortunate to work closely with two creative, yet vastly different machinists of the mid-19th century—J.B. Parker and E.B. Bigelow.