Flexible Supercapacitors. Группа авторов
Чтение книги онлайн.
Читать онлайн книгу Flexible Supercapacitors - Группа авторов страница 18
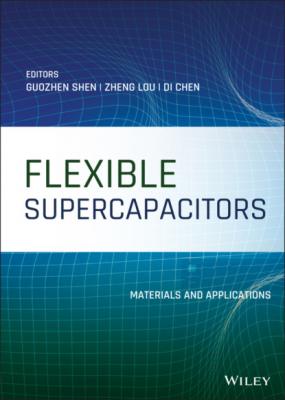
Figure 2.3 Typical fabrication methods of 1D parallel fiber SCs: (a) Schematic illustration of the fabrication process of the fiber SCs by embedding in pre‐strained stretchable substrate, (b) CV curves of the stretchable devices under stretching and folding.
Source: Reproduced with permission [56]. © 2017, Wiley‐VCH.
(c) Schematic illustration of the fabrication process of the fiber SCs by twisting sandwich fiber with double side electrode, (d) CV curves measured during successive stretch, twist, release and untwist process.
Source: Reproduced with permission [57]. © 2016, American Chemical Society.
Different from the first embedded method, the second parallel SCs always employ the elastic materials as the stretchable substrate. In 2016, Choi et al. introduced stretchable SCs with sandwich fiber, the schematic illustration of the fabrication process was presented in Figure 2.3c [57]. The assembled method can be summarized as four steps: (i) Preparation of fiber shaped substrate. The dielectric silicone rubber (Ecoflex 0030) was processed as a sheet with a length of 30 mm by the conventional reaction of commercially available resins in a rectangular and then cut into ∼2 mm thick. (ii) Pre‐stretching the fiber shaped silicone rubber. The as‐prepared core fiber was stretched along the axial direction by 300% of its length. (iii) Covering electrode material on the surface of the core fiber. CNT aerogel sheets that extract from a multiwalled carbon nanotube (MWNT) forest served as electrode materials, which is attached on both sides of the silicone rubber fiber. The direction normal to the CNT electrode was coved with a PU film to prevent electrical shortage by residual CNT bundles during CNT wrapping. The strong adhesion between the CNT electrode and the silicone rubber fiber was guaranteed by continual dropping ethanol during CNT wrapping, which also protects the CNT surface from delamination. Then, the PU mask was mechanically removed from the silicone rubber fiber with CNT coat. 4: Release the fiber. The CNT electrode materials after release archived a uniform waved electrode. The electrical resistance of the CNT electrode materials is about 179 Ω cm−1 at the CNT loading of 2.31 mg cm−2 for each side, which is benefit to the electrochemical performances of the stretchable fiber SCs. Figure 2.3d showed the CV curves of the fiber SCs measured during successive stretch, twist, release and untwist process. Importantly, when applied a successive stretch, twist, release and untwist deformation during charge and discharge, the electrochemical performance of the fiber devices didn't change. The stretch test also showed an imperceptible nuance under various strains ranging from 0% to 200%.
2.2.1.2 Fabrication of Stretchable Twisted SCs
The preparation technology of the stretchable twisted SCs has been well developed in the recent years. Several kinds of strategies toward stretchable twisted SCs were summarized in Figure 2.4. Figure 2.4a showed the schematic illustration of a fabrication method through twisting two pre‐stretched elastic wires wrapped with aligned CNT sheet as electrode materials [58]. First, the elastic wire was stretched to 100%. Then, the aligned CNT sheet was transformed to the pre‐stretched wire. Next, two poly (vinyl alcohol) (PVA)/H3PO4 coated elastic wires with CNT electrode were twisted. After releasing the pre‐strain wire to its nature state, the stretchable twisted SCs were prepared, which showed extremely high strain (>300%) without detrimental effects to the conductivity of the electrode. Figures 2.4b exhibited the top‐view and cross‐section SEM (scanning electron microscope) images of the twisted SCs. From the SEM images, we can see that the thickness of PVA/H3PO4 and CNT sheets were 50 and 10 mm, respectively. The electrochemical performances of the fabricated twisted SCs were also carried out, as displayed in Figure 2.4c. The inset is the photos of the twisted devices under various strains ranging from 0% to 370%. The normalized capacitance (a ratio of the capacitance under a specific strain to that at 0 strain) as a function of the tensile strain showed a 13% of increase for the device based on CNT wrapped elastic wire electrodes as the tensile strain increased from 0% to 250%. This can be explained by the strain‐induced enhancement in the contact between the two twisted electrodes upon stretching. When the tensile strength was above 250%, a slight decrease in the capacitance was appeared caused by the imperfect contact between CNT and/or PVA/H3PO4, but it was still 10% higher than the initial capacitance. Moreover, in this paper, the CNT/PEDOT‐PSS (poly (3,4‐ethylenedioxythiophene)‐poly (styrene sulfonate)) based stretchable twisted SCs were also fabricated using the same technology, which depicted an excellent capacitance retention under different stretching state, indicating that it's a feasible method to large‐scale produce different kinds of stretchable twisted SCs.
Figure 2.4 (a) Schematic illustration of fabricating twisted SCs by wrapping aligned CNT sheet around a pre‐stretched elastic wire. (b) Top‐view and cross section SEM images of the fiber SCs. (c) Changes in the normalized capacitance under stretching.
Source: Reproduced with permission [58]. © 2014, Wiley‐VCH.
(d) Schematics of the fabrication procedures for stretchable fiber SCs by twisting the devices. (e) Optical microscopy images the fiber devices. (f) Specific capacitance of the fiber SCs under stretching.
Source: Reproduced with permission [35]. © 2014, Wiley‐VCH.
Another group of stretchable twisted SC have no ability of stretchability itself, with the whole devices twined around the elastic substrate. For example, Xu et al. proposed a fabrication method by using spandex fiber as the substrate (Figure 2.4d) [35]. Specifically, a fiber‐shaped SC was fabricated by twisting two CNT based fiber electrodes. Then, next, spandex fiber was pre‐stretched to 100% with a PDMS coat to prevent influence from acidic H2SO4‐PVA gel electrolyte. And then the fiber‐shaped SCs were “glued” onto the spandex fiber. When the substrate was released, the SCs with stretchability over 100% were accomplished. Figure 2.4e showed the photography of the serpentiform stretchable SCs. A slightly enlarged of the CV loop areas suggested the enhanced capacitance when the SC was stretched to a large strain of up to 100%. Moreover, the specific capacitance of the fiber SCs under stretching (Figure 2.4f) also surpassed those of the initial unbuckled SCs after 20 cycles of deep stretching. The outstanding stretchability can contribute to the buckled structures formed after releasing the strain. This fabrication method could make most of the twisted SCs stretchable, but the devices and the stretchable substrate are two separate parts, which is unfavorable to keeping the electrochemical performances under repeated deformation. Nevertheless, more advanced technologies for solving the above‐mentioned problems