Flexible Supercapacitors. Группа авторов
Чтение книги онлайн.
Читать онлайн книгу Flexible Supercapacitors - Группа авторов страница 19
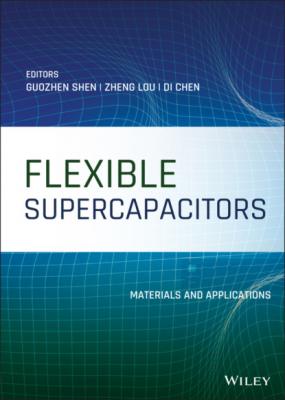
2.2.1.3 Fabrication of Stretchable Coaxial SCs
Among the three structures of fiber SCs, the fabrication of stretchable coaxial SCs is the most complicated, but this configuration makes the device more integrated than the parallel and twisted structures [59]. The biggest difficulty lies in the fabrication of sheath/shell‐like electrode (outer electrode). To date, many efforts have been devoted to the development of novel coaxial SCs. For example, Lee et.al proposed an assembly method by wrapping separator and carbon nanofiber (CNF) film on the surface of the core fiber electrode, but it makes the contact resistance large and the electrode materials waste [44]. In contrast to this structure, Peng's group reported a stretchable coaxial SCs that fabricate layer by layer, from inside to outside, in sequence of inner electrode, gel electrolyte and outer electrolyte without separator, as shown in Figure 2.5a and b [36]. Figure 2.5a showed the schematic illustration of the corresponding fabrication process. An elastic fiber was used as stretchable core fiber substrate. To start with, a coat of PVA‐H3PO4 gel electrolyte was made on the surface of the elastic fiber. Next, the aligned CNT sheets were wrapped around the gel electrolyte coted elastic fiber as the inner electrode. Followed by coating the second layer of electrolyte as separator and wrapping with another CNT sheet as the outer electrode. Finally, the third layer of gel electrolyte was spread around the outer electrode. The fabricated SCs exhibited a specific capacitance of 20 F g−1, mass energy of 0.515 W h kg−1and power densities of 421 W kg−1. Figure 2.5b presented the CV profiles of the stretchable coaxial SCs with increasing strains. The overall stretchability could reach as high as 100% with a good specific capacitance retention. The specific capacitance was remained above 90% after 1000 charge‐discharge cycles when applied a strain of 75%, showing a promising stability under deformation. Although they achieved the goal of produce stretchable coaxial SCs, unfortunately, reports so far on high performance have been very limited. Great efforts should also be focused on promoting the electrochemical properties of stretchable coaxial devices.
Figure 2.5 Schematics of the fabrication procedures for coaxial SCs and corresponding electrochemical performances at different tensile strains. (a, b) Pre–stretching substrate and electrode.
Source: Reproduced with permission [36]. © 2013, Wiley‐VCH.
(c, d) Over‐twisting the SCs device into a helical structure. (e) Areal specific capacitance variations with scan rates.
Source: Reproduced with permission [60]. © 2016, Wiley‐VCH.
Recently, Yu et al. fabricated a stretchable helical coaxial asymmetrical SCs with high energy and power density by employing two CNT@MnO2 and CNT@PPy as positive and negative electrode respectively without a stretchable polymer core substrate [60]. Figure 2.5c depicted the schematics of the fabrication procedures. To start with, a CNT fiber was decorated with MnO2 nanomaterials, which served as inter electrode. Next, the gel electrolyte was coated around the CNT@MnO2 fiber. Then the CNT@PPy film was wrapped on the gel electrolyte as the outer electrode. The cross‐section SEM images of asymmetric coaxial SCs at 0% and 50% strain were displayed in Figure 2.5d. From the SEM images, we can clearly see the two concentric circular areas, indicating the core‐sheath structures of the fabricated SCs. And the SCs possess a helical structure formed by over‐twisting the devices which make the SCs stretchable. Owing to the utilization of two different electrode materials, the fabricated SCs exhibited a specific capacitance of 60.435 mF cm−2 at the scan rate of 10 mV s−1 and a high energy density of 18.88 μW h cm−2 with an extended potential window of 1.5 V. The specific areal capacitance curves in Figure 2.5e showed a slightly decrease when the SC was stretched to 20%. Despite the limited stretchability of the coaxial SCs, the electrochemical performance was much improved, paving a great support to the real application of the stretchable SCs.
2.2.2 Planar Stretchable SCs
Stretchable 2D planar SCs with excellent properties of small size, low weight, excellent lifespan, high security and easy integration have become a preferred choice as energy storage to power the wearable electronics [37, 61–63]. There are two main categories including layer by layer sandwich structure and micro supercapacitors (MSCs). The fabrication method of the 2D planar stretchable SCs is similar to 1D fiber shaped SCs. One is via embedding rigid independent devices to the stretchable substrate or establishing serpentine interconnects between rigid devices to realize stretchability. Another one is replacing the rigid unit by stretchable component. In this section, we will introduce the typical fabrication method reported during the last few years.
2.2.2.1 Fabrication of the Stretchable Planar SCs with Sandwich Structure
Sandwiched planar SCs is the most developed and widely applied structure in the field of the SCs. The main issues that impede the successful fabrication of stretchable SCs is how to make a tight connection between electrode materials and elastic substrate. As early as 2009, Yu et al. proposed a strategy via directly transferring the single‐walled carbon nanotube (SWCNT) film to pre‐strained PDMS substrate [64]. It's worth mentioning that the PDMS substrate was treated by UV light to forming a strong bong with SWCNT film. The fabrication process was presented in Figure 2.6a. Figure 2.6b showed the SEM images of the SWCNT film with buckled microstructures, which directly contribute to the stretchability of the fabricated SCs. Figure 2.6c displayed the CV profiles of the stretchable SCs measured at 30% strain. From the CV curves, we can see that the electrochemical performance of the stretchable SCs remains unchanged even under 30% applied tensile strain. But the utilization of a polymeric separator restricted its stretchability. To overcome this problem, Niu et al. reported stretchable SCs based on periodically sinusoidal oriented SWNT film without separator and liquid electrolyte using the same pre‐strained‐buckled‐release method, which showed increased stretchability of over 120%.
Most of the deformable substrate used in the field of stretchable SCs is PDMS. In 2014, Xie et al. reported a flat Ni foam based stretchable all‐solid‐state SC with wavy shaped polyaniline (PANI)/graphene electrode [65]. Figure 2.6d showed the schematics of the fabrication process for fabricating the PANI/graphene electrodes based stretchable SCs. First, a flat Ni foam with a thickness of 200 mm was manually made into a wavy shape, next, the porous graphene was synthesized on the buckled Ni foam via atmospheric pressure chemical vapor deposition (CVD). Then the graphene coated Ni foam was put in a solution of 3 M HCl to etch nickel foam to obtain wavy‐shaped graphene film. In order to improve the electrochemical performance of the SCs, the PANI was deposited on the wavy shaped graphene film. Finally, two PANI covered graphene films with PVA/H3PO4 wall were encapsulated into Elastic substrate (Ecoflex). Figure 2.6e depicted